Droplet formation in AlCrN cathodic Arc PVD Coatings
- Christos Pernagidis
- Apr 14
- 2 min read
Updated: Jun 6
Introduction
Cathodic arc physical vapour deposition (arc-PVD) is the preferred method for applying hard coatings, such as AlCrN, to cutting tools. However, the inherent formation of macroparticles, or droplets, during this process presents challenges, particularly regarding surface roughness and adhesion. Understanding droplet formation is crucial for optimising AlCrN coatings deposited from Al70Cr30 cathodes onto WC or HSS substrates. I want to explore the mechanisms of droplet generation, the factors that influence their behavior, and practical strategies for mitigating their impact.

Mechanisms of droplet generation
The high-current arcs in arc deposition create localised high-power-density spots on the cathode, leading to rapid melting and vapourisation. This results in the ejection of molten material as macroparticles due to explosive emission. These droplets subsequently travel with the plasma toward the substrate, where they may agglomerate before embedding in the coating or rebounding, thus creating surface defects. The extent of droplet formation is heavily influenced by the thermophysical properties of the cathode material; lower-melting-point materials, such as aluminium, are particularly susceptible to droplet ejection.
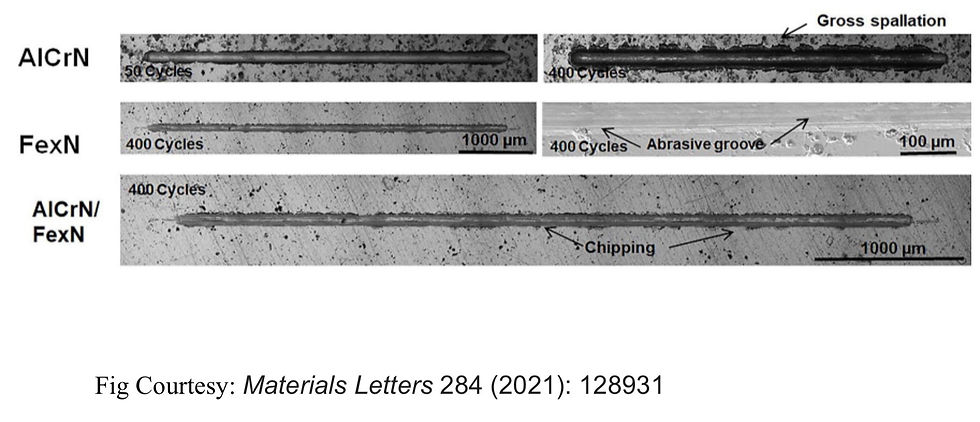
Influence of Al:Cr target composition
The Al/Cr ratio and the method of target fabrication play a significant role in determining droplet behaviour:
- Aluminium content: Increasing aluminium content in the cathode results in smaller droplet sizes but may lead to a higher frequency of droplets, which can negatively affect surface roughness.
- Alloy vs. composite targets: Homogeneous alloyed targets provide consistent arc erosion and significantly reduce droplet formation. In contrast, composite targets with segregated Al and Cr phases may exhibit uneven arc behavior, increasing droplet emissions.

Process parameters affecting droplet formation
- Arc current: Higher currents increase cathode spot energy, producing larger and more numerous droplets. Conversely, lower currents can effectively reduce droplet density.
- Chamber pressure: Increasing nitrogen pressure enhances droplet scattering and evaporation, reducing surface defects.
- Magnetic fields: Utilizing magnetic arc steering minimises prolonged cathode spot dwell, thus reducing the ejection of larger droplets. Additionally, filtered arc sources can efficiently separate droplets from the plasma, yielding cleaner coatings.
- Substrate bias: Applying a higher negative bias (ranging from -50 V to -200 V) enhances ion bombardment, facilitating the dislodgment of loosely adhered droplets and achieving a smoother coating surface.

Strategies for droplet mitigation
- Macroparticle Filters: Magnetic filters effectively separate droplets from the plasma stream, improving coating smoothness.
- Magnetic Arc steering: Employing precise electromagnetic control of arc motion reduces localised overheating and droplet generation.
- Optimized target design: Dense, homogeneous alloyed AlCr targets are superior to porous or composite targets in minimising droplet emissions.
- Controlled Arc parameters: Lowering the arc current, adjusting the chamber pressure, and optimizing the bias voltage are essential for managing droplet incorporation.
By strategically fine-tuning material selection and deposition parameters, we can optimise AlCrN arc-PVD coatings to minimise macroparticle-related defects, thereby ensuring enhanced coating performance for various industrial applications.
Comments