ARC COATING
The technique of arc evaporation emerged from welding technology. In the arc process, the electrically conductive evaporation material is placed horizontally or vertically in a vacuum chamber as a solid plate. It acts here as a negative potential and creates an arc when it comes into contact with the anode.
A small point a few micrometers in diameter appears on the surface of the evaporation material. There, only at this point, does the material vaporize directly and form a highly concentrated plasma in the form of a steam lobe. The material to be coated is guided through this steam lobe. This creates a homogeneous, durable coating.
ADVANTAGES OF THE ARC PROCESS
Homogeneous coating and good reproducibility
Good adhesion, reflectivity and corrosion protection
If you compare the ARC process with magnetron sputtering, arc evaporation is often more efficient.
The most common areas of application in arc PVD are tool coating and the coating of components.
​
As a supplier with many years of experience and contacts to many manufacturers, we are happy to help you with the selection of materials
A SELECTION OF HIGH QUALITY COATING MATERIALS
We deliver according to your specifications

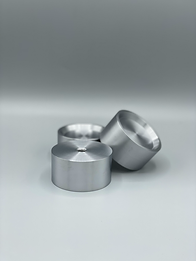







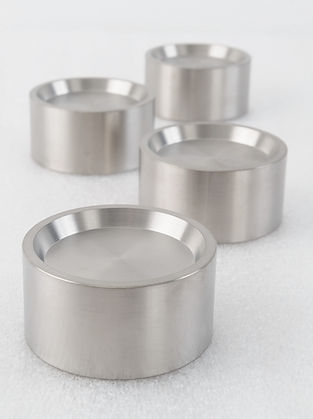
ARC CATHODES
AVALUXE supplies ARC cathodes for arc evaporation. The ARC process is used as standard in the production of nitridic hard material coatings and also offers many advantages for other types of coatings.
Typical areas of application are the coating of tools for machining, forming and die casting, as well as the coating of various components for wear protection.
ARC COATING
The technique of arc evaporation emerged from welding technology. In the arc process, the electrically conductive evaporation material is placed horizontally or vertically in a vacuum chamber as a solid plate. It acts here as a negative potential and creates an arc when it comes into contact with the anode.
A small point a few micrometers in diameter appears on the surface of the evaporation material. There, only at this point, does the material vaporize directly and form a highly concentrated plasma in the form of a steam lobe. The material to be coated is guided through this steam lobe. This creates a homogeneous, durable coating.
ADVANTAGES OF THE ARC PROCESS
-
Homogeneous coating and good reproducibility
-
Good adhesion, reflectivity and corrosion protection
In comparison to to the magnetron sputtering, the ARC process is often more efficient.
The most common areas of application in arc PVD are tool coatings and the coating of components.
​
As a supplier with extensive experience and contacts to many manufacturers, we are happy to help you with the selection of materials
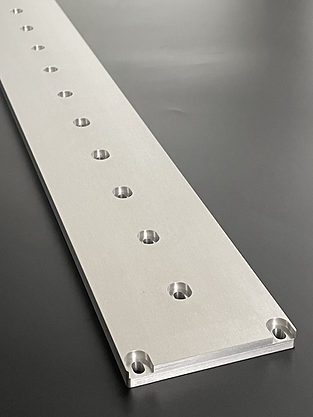
SPUTTER TARGETS
Avaluxe is your expert for coating and evaporation materials and supplies all common materials for sputter-target coating from the areas
​
-
Architectural glass coating
-
Roll-to-roll coater
-
Selective absorber layers
-
Photovoltaic
-
Tool coating
-
Decorative coating and optics
​
A list of our standard materials in the form of planar targets and tube targets can be found a little below. We sift through all the important sputter target manufacturers and decide on the right material.
SPUTTER PROCEDURE
So-called magnetron sputtering (cathode sputtering) is a physical process in which atoms are detached from a solid by ion bombardment and become gases.
In coating technology, this process is used to atomize a material, which is then deposited on a substrate and becomes a solid layer.
​
In the sputtering process, unlike the ARC process, the layer material is not melted, but is converted directly from the solid to the gaseous state. The advantage is that there are no bumps and an extremely smooth coating is achieved.
Almost any material can be coated and there are also many possible combinations of the various materials. The sputtering process uses lower temperatures than the PVD process.
SPUTTER TARGET APPLICATION
Sputtering has a wide range of uses, especially in industry. In general, the range of materials that we can supply you with is very large - the classic ones are titanium, tungsten and chrome.
​
​
Areas of application are for example
-
Material- and surface finishing of mirrors
-
Car headlights
-
Optics: a thin-film polarizer or heat protection glass