Why beautiful PVD finishes start with hard science
- Christos Pernagidis
- May 27
- 4 min read
Updated: Jun 11
If you think color is just a design choice, think again—developing a decorative PVD coating that actually performs takes materials engineering, vacuum physics, and a serious R&D mindset.
Introduction: more than just a beautiful finish
Modern consumers are increasingly drawn to products that feature unique and eye-catching finishes. Decorative Physical Vapor Deposition (PVD) coatings have emerged as a premium solution, offering both stunning aesthetics and outstanding durability. Unlike traditional chrome plating, which is limited in color range and performance, PVD coatings provide a nearly limitless palette of hues, along with enhanced hardness, wear resistance, and environmental sustainability.
But creating a custom decorative PVD color isn’t just a matter of matching a swatch. It requires deep scientific understanding, engineering precision, and a methodical development approach. For business leaders and product developers, recognizing the complexity of this process is essential to ensuring long-term value and product success.
Understanding substrate-coating interactions
The substrate material plays a pivotal role in the PVD coating process. During deposition—which occurs at elevated temperatures in a vacuum environment—substrate compatibility is critical. Metals generally tolerate higher temperatures, while plastics like ABS or polycarbonate can deform or outgas at 95–130 °C. To coat plastics, engineers must adjust process parameters or apply low-temperature PVD technologies.
Surface preparation is equally vital. Contaminants, surface roughness, or improper pre-treatment can compromise adhesion. Since PVD coatings are ultrathin (often 0.2–0.5 µm), they conform to the microstructure of the substrate. A polished base yields a glossy finish; a matte substrate delivers a muted effect. The final appearance, adhesion strength, and durability all hinge on preparing the substrate correctly.
Different substrates also require tailored coating architectures. For example, a corrosion-prone metal might need an adhesion layer beneath the decorative topcoat. Chrome-plated plastics often demand extra steps to ensure compatibility with the PVD layers. Recognizing these interactions early in development is key to avoiding costly rework or performance issues down the line.
Engineering the color: materials, process, and coating architecture
In PVD technology, color is engineered through the controlled interaction of materials and process parameters. It starts with selecting the right target material—metals or alloys—and introducing reactive gases in the vacuum chamber. For instance:
Titanium + Nitrogen = TiN (gold tone)
Titanium + Nitrogen + Carbon = TiCN (rose-gold)
Zirconium + Oxidizing gas = Blue, grey, champagne, or graphite shades
The hue depends on both the compound formed and the stoichiometric balance. Even minor changes in gas flow, power settings, or pressure can alter the outcome. For interference-based colors like blues and purples, film thickness matters: subtle variations affect how light reflects off the surface, resulting in vivid or inconsistent coloration.
On 3D parts, these effects become more pronounced. Engineers must optimize thickness uniformity through racking strategies or by engineering coatings to be optically opaque. Without this, colors may shift across complex geometries.
Coating architecture also influences results. A multilayer structure might combine adhesion, color, and protection layers to meet all performance criteria. Each additional layer introduces complexity—more stress, longer deposition times, and additional interface bonding challenges. Balancing these parameters is a key strength of experienced development teams.
Testing, validation, and iterative development
After coating development, rigorous testing ensures the product meets quality and performance standards. Test methods include:
Abrasion tests (e.g., steel wool scrub)
Adhesion tests (e.g., cross-cut or tape test)
Chemical resistance (e.g., exposure to household cleaners)
Corrosion and UV aging
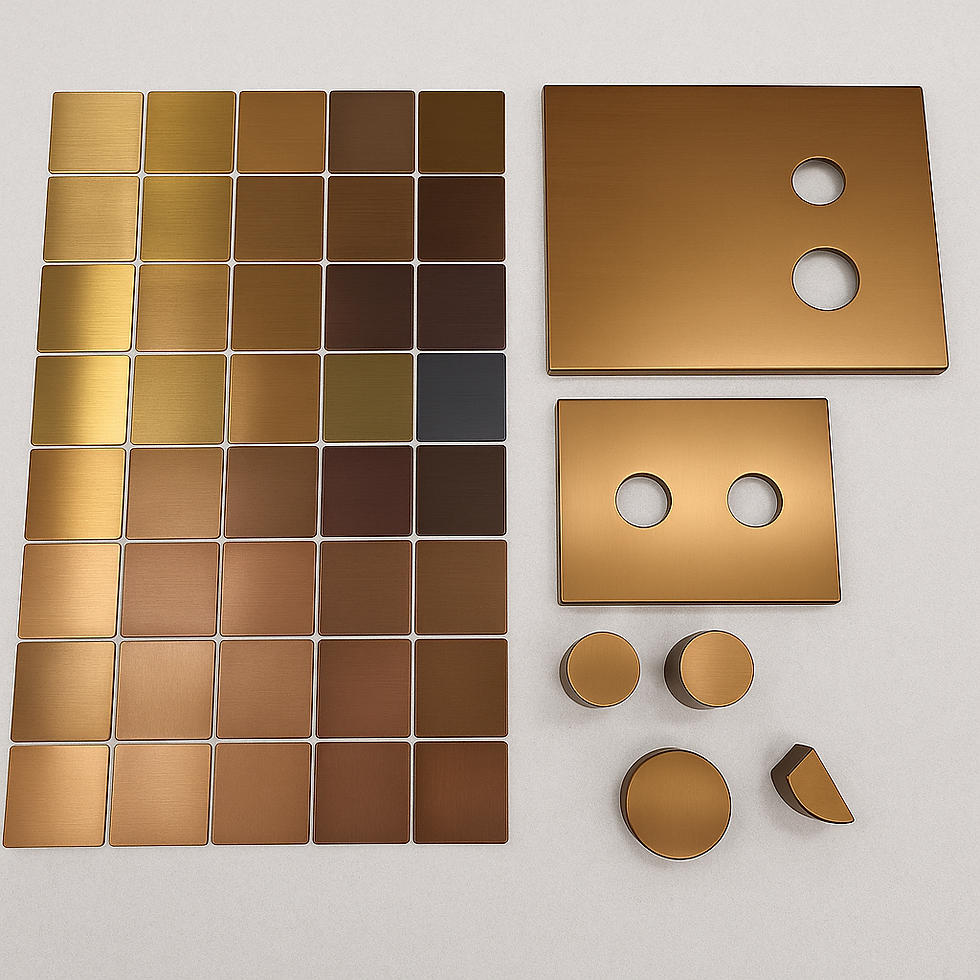
These tests confirm that coatings don’t just look good—they endure real-world conditions. High-quality PVD finishes can withstand thousands of abrasive strokes, resist color fading, and maintain adhesion over time.
Most coatings require multiple iterations. A failed adhesion test might prompt a change in the base layer or surface prep. Color shift under UV exposure might demand a tweak in gas ratios. Each cycle adds data and insights, improving future development speed and reliability.
Advanced labs use SEM (scanning electron microscopy), nano-indentation, and spectrophotometry to quantify performance and color accuracy. These tools support precise optimization and build a database of proven solutions.
Long-term benefits: investing in quality and expertise
For decision-makers, custom PVD development is an investment in brand value. A well-executed finish enhances product perception, reduces warranty claims, and boosts customer satisfaction. It also leads to:
Process repeatability
Lower rejection rates
Faster time-to-market for future designs
Adaptability of validated coatings across product lines
Skipping the development phase or cutting corners often backfires—coatings fail, customers complain, and rework costs skyrocket.
By partnering with experienced PVD specialists, companies can avoid these risks and confidently introduce new, high-quality products. This collaboration brings materials science, engineering know-how, and aesthetic design into one cohesive process.
Conclusion: hard science, beautiful results
Custom decorative PVD coatings are not just a trend—they’re an engineering solution wrapped in visual appeal. The intersection of material choice, vacuum technology, surface science, and precise process control is where true innovation happens. And that’s why beautiful finishes don’t come from guessing—they start with hard science.
Optimized PVD coatings deliver more than looks. They bring consistency, durability, and scalable success to your product line. In a competitive market, that’s more than decorative—it’s strategic.
Comments